COVID-19 prompts increased shift towards 3D printed medical material

3D printing in the medical field is helping to save lives in many different ways.
With 3D printed material becoming increasingly common in the medical field, the onset of COVID-19 has sparked even further demand for materials made in this revolutionary fashion.
Low supplies and humanity’s desire for solutions to help prevent the spread or mitigate COVID-19 symptoms has led to a sudden rise in research and development of 3D printed medical supplies.
Also known as additive manufacturing, 3D printing is a digital technology that creates customisable products with greater precision, more efficiency and at a lower cost than traditional processes.
Using artificial intelligence, 3D printing also makes it possible for new designs to be created that were previously unattainable with more time consuming, less precise and more wasteful traditional manufacturing.
Medical technology company Osteopore’s (ASX: OSX) executive director Geoff Pocock said 3D printing was also advantageous because it simplified the supply chain.
He added it was particularly preferable at the moment with COVID-19 disrupting manufacturing globally, with disruption of component supplies having major downstream implications for manufacturing and production around the world. .
Because traditional plants have been closed, companies who make materials via traditional manufacturing have had to look elsewhere for essential parts and components, which can have complex specifications.
In comparison, 3D printing can require just one bulk material to make the entire product, which in Osteopore’s case is its regulatory approved bioresorbable polymer for safe use inside the body.
Mr Pocock pointed out that 3D printing has two other major advantages – with highly precise structural accuracy and the ability to customise a product to an individual patient.
As an example, he said a CT scan of a head injury could be used to create a one-off product for a specific individual. Osteopore can then create a specific product that not only matches the exact shape of the patients’ injury, but also create the micro-structure of pores, channels and associated product architecture necessary for regenerative bone healing.
“It’s that combination of macro-structure and fine detail that can’t be done via traditional manufacturing methods,” Mr Pocock added.
3D-printing optimises ventilators and masks
Meanwhile on the COVID-19 frontline, ventilators are critical in treating COVID-19 patients who have developed acute respiratory distress syndrome (ARDS) and due to the soaring number of cases, many countries are finding these in scarce supply.
This led to Belgian doctors coming up with an idea for a novel 3D printable valve mechanism that enables a mechanical ventilator to be used by two people instead of one.
Belgian engineers and no2covid.com co-founders Dirk Wenmakers and Philippe Caers ran with the idea and developed a 3D printed device to be trialled.
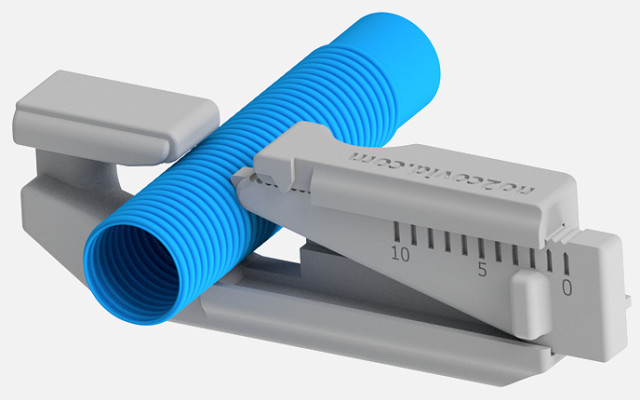
3D printed valves by no2covid.com are quadrupling the capacity of ventilators at a hospital in Geel, Belgium.
Dr Luc Janssen from Belgium’s Geel hospital said the disposable and easy to use valve can be used to split a ventilator so it can then be used by two patients and adapted to suit each patient’s airflow requirements.
Additionally, 3D printing specialist Materialise revealed it had another solution to the ventilator shortage and has created a 3D printed oxygen non-invasive PEEP (NIP) mask connector, which can convert equipment found in most hospitals into a mask that assists with breathing by creating positive pressure in the lungs.
According to Materialise, the assembled masks enable clinicians to reduce pressure on ventilator supply by decreasing the time patients may require a mechanical ventilator.
Materialise anticipates the device will be available for hospitals imminently.
3D printing for medical sector outside of COVID-19 need
Outside of COVID-19, 3D printed medical supplies have already helped save and improve lives in a way never previously imagined.
Osteopore is a company that has managed to achieve this with its 3D-printed and regulatory approved medical implants to facilitate natural tissue regeneration.
The company 3D prints scaffolds using a proprietary polymer formulation. The material is designed to dissolve over time and leave behind healthy bone tissue.
Osteopore claims these scaffolds can “significantly” reduce post-surgery complications that are often associated with permanent implants.
The company’s Osteoplug is a bioresorbable implant that comprises a porous matrix enabling it to be saturated with marrow, blood and nutrients to encourage bone regrowth and remodelling.
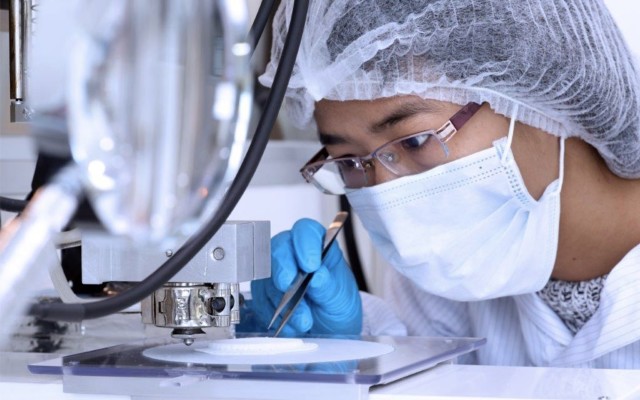
Osteopore’s 3D printed products are FDA, TGA and CE Mark cleared, and have been used successfully in over 20,000 surgical procedures.
It can be implanted without screws and is used for healing burr holes resulting from neurosurgery.
Osteopore has designed its Osteomesh to repair fractures and fill surgical defects in the face, skull, neck, jaw and head.
The mesh provides a rigid and flexible scaffold to support bone during growth. It then degrades once bone regeneration has occurred.
Meanwhile, Osteopore’s Osteostrip is biodegradable and designed to fill the void following a craniotomy, which involves removing bone from the skull to expose the brain.
It can fill the void between the cranial flap and cranium without the need for screws and provides high structural integrity and long-term integration with surrounding bone.
In a recent market update, Osteopore chief executive officer Goh Khoon Seng said the company is experiencing “increasing demand” for its unique 3D printed bioresorbable implants despite COVID-19.
Bioprinting organs
Taking it a step further than Osteopore’s 3D printed bone regeneration technology is bioprinting.
Berkeley researchers from the University of California recently created a device that has greater potential to 3D print human tissue, bone, blood vessels, organs and even food.
During a 3D printing session, which can be lengthy, living cells deteriorate because they require complex and specific temperature and chemical conditions to survive.
However, the Berkley researchers have developed a device that uses identical printers to create multiple layers simultaneously. The layers are then stacked on top of each other to form a 3D structure.
Each layer of cells that is added to the structure is also cryogenically frozen to preserve cell life.
“Right now, bioprinting is primarily used to create a small volume of tissue,” Berkeley Professor of mechanical engineering Boris Rubinsky said.
“The problem with 3D bioprinting is that it is a very slow process, so you can’t print anything big because the biological materials will deteriorate by the time you finish.”
“One of our innovations is that we freeze the material as it is being printed, so that the biological material is preserved, and we can control the freezing rate,” Prof Rubinsky explained.
Although not there yet, part of the technology’s aim is to eventually 3D print organs with more than 112,000 people in the US currently on the country’s transplant list.