Breakthrough graphene technology could create next generation of super computers

Scientists have developed a new method to create graphene interconnects for faster computers, but the technology could take a while to be adopted by the semiconductor industry.
A new method could make graphene a key component in the creation of faster, smaller and lighter high-performance computers, according to scientists.
Although, resistance from the multi-billion-dollar semiconductor industry could mean a long road to making this development a reality.
Electric and computer engineering researchers at the University of California Santa Barbara (UCSB) have recently developed a method to implement high-conductivity, nanometre-scale doped multilayer graphene (DMG) interconnects that are compatible with high-volume manufacturing of integrated circuits.
According to UCSB, the physical limitations of using interconnects made of copper poses a “fundamental threat to the $500 billion semiconductor industry” and graphene could potentially be the solution for the world’s interminable demand for faster, lighter and cheaper devices.
Yet, Pitt Street Research managing director Marc Kennis told Small Caps that switching materials in semiconductors is “not easily done” and is “something that will take years to do” because of the “high stakes involved”.
Semiconductors
A semiconductor falls in between a conductor, such as copper, which conducts electricity and an insulator like glass, which resists electricity.
Their conductivity can be altered with the introduction of impurities, called doping, to meet the needs of the electronic component it is being used in.
Semiconductor chips, more commonly referred to as microchips, contain billions of transistors and are found in a range of technologies including computers, smartphones, appliances, gaming hardware and medical equipment.
The more transistors on a chip, the faster it can work. In addition, production costs and the price of the product is lowered.
The continuous development of semiconductors has changed the way we live – electronic devices are now lighter, less bulky and have greater features.
Copper limitations
Interconnects, which are fundamental components that link the billions of transistors on microchips, have been made of copper for more than 20 years.
However, the metal has some basic physical limitations when electrical components that incorporate it shrink to the nanoscale.
According to UCSB Professor Kaustav Banerjee, as the dimensions of copper wires are reduced, their resistivity to electricity increases.
“Resistivity is a material property that is not supposed to change, but at the nanoscale, all properties change,” he said.
As the resistivity increases, copper wires generate more heat, which reduces their current-carrying capacity.
According to UCSB, this is a problem that poses a “fundamental threat” to the semiconductor industry, which graphene has to the potential to solve.
Though, the biggest obstacle is finding a way for graphene micro-components to be “manufactured on-chip, on a large scale, in a commercial foundry”.
Mr Kennis agrees there are many limitations that need to be overcome before graphene can be introduced into the manufacturing process for semiconductors.
“For a material, it’s probably one of the best materials you could use but there’s a lot of research still to be done,” he said.
“You can use the material in a university or facility testing environment but transferring it to a mass volume production facility – that’s a totally different ball game,” Mr Kennis said.
Breakthrough technology
Graphene is considered the strongest, thinnest and by far most reliable electrically conductive material discovered in the world to-date.
Since its discovery in 2004, scientists have been working to develop commercially-scalable applications for this high-performance material and UCSB researchers now believe it has the potential to be an extremely promising material for interconnects.
Professor Banerjee said the semiconductor industry “will only move forward with it if you find a way to synthesise graphene directly onto silicon wafers”.
The problem is, to synthesise something at the ‘back-end’ – that is, after the transistors are fabricated – you face a thermal budget that can’t exceed a temperature of about 500 degrees Celsius.
“If the silicon wafer gets too hot during the back-end processes employed to fabricate the interconnects, other elements that are already on the chip may get damaged, or some impurities may start diffusing, changing the characteristics of the transistors,” UCSB stated.
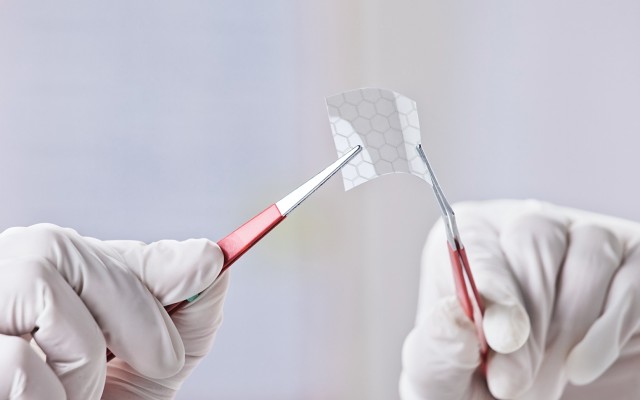
UCSB’s research shows graphene interconnects have the potential to create faster, smaller, lighter, more flexible and more reliable integrated circuits.
After a decade of research, Professor Banerjee and his lab have now developed a unique pressure-assisted solid-phase diffusion method for directly synthesising a large area of high-quality multi-layer graphene on a typical dielectric substrate used in the back-end CMOS (the standard industry process for making integrated circuits) process.
This diffusion method involves applying pressure and temperature to two different materials that are in close contact, so they diffuse into each other.
The UCSB team began by depositing solid-phase carbon in the form of graphite onto a deposited layer of nickel metal of optimised thickness. Then, heat (about 300 degrees Celsius) and pressure was applied to the graphite powder to help break down the graphite.
The high diffusivity of carbon in nickel allows it to pass rapidly through the metal film, and the carbon atoms then recombine on the other surface of the nickel closer to the dielectric substrate, forming multiple graphene layers.
Lead author of UCSB’s research paper describing the novel process, Junkai Jiang said the lab was able to “optimise the nickel thickness and other process parameters to obtain precisely the number of graphene layers we want at the dielectric surface”.
“Because our process involves relatively low temperatures that pose no threat to the other fabricated elements on the chip, including the transistors, we can make the interconnects right on top of them,” Mr Jiang said.
In summary, UCSB’s research shows graphene interconnects have the potential to create faster, smaller, lighter, more flexible, more reliable and more cost-effective integrated circuits.
Challenges of implementation
Sounds good in theory, but how far off are we from replacing copper for this breakthrough technology? Possibly more than a decade, according to Mr Kennis.
“[Graphene] does have some clear advantages, but that doesn’t always mean you can implement it in new products,” he said.
“It could take more than 10 years to get that sort of squeeze into existing facilities.”
Mr Kennis said while the semiconductor industry is innovative, it is also “extremely conservative when it comes to new production methods, because of the money involved”.
“The conductivity of the material is such that you’ll get a lot faster processors with lower bar consumption so that’s a very obvious benefit, but I’m not sure what the manufacturing costs would be using graphene in mass production … It’s a cost benefit analysis,” he said.
“To change one material, it can affect the whole performance of the chip. So, what happens is that [the industry is] usually very reluctant to start using new materials unless it’s developed to the point where it can’t be developed any further, and the equipment used by the manufacturer fits into the existing machines or the existing production line,” Mr Kennis said.
He used Intel as an example of a tech company that “pumps out billions of chips each year and make a lot of money doing that” so would “never implement any new technology unless its been thoroughly tested in test facilities and their own facilities”.
“As soon as you replace something in the production line, you’re upsetting first of all, revenue stream, and you’re introducing risk into the production line,” Mr Kennis added.
He noted that the substitution of aluminium by copper took a number of years as well.
“Even if you’ve solved everything and we get faster chips that can be smaller and lower in energy consumption, how much will it cost to manufacture one of them in mass production?”
“If the price is too high, then consumers won’t buy them or companies won’t buy them … all of that typically leads to long lead times for any new material or technology to make it into production,” Mr Kennis said.
So, it might be a number of years before any substitution in a manufacturing process will take place.
But when it does, there are a number of ASX-listed graphene and graphite companies that could benefit.