3D printed lithium-ion batteries are now a reality

3D printing of lithium-ion batteries is now possible thanks to researchers at Duke University.
Imagine a world where lithium-powered consumer products can be created in any shape or size – as could the batteries that keep them running.
This is currently not achievable on a commercial scale, mainly due to lithium-ion batteries only being available as a generic square or cylindrical shape and most devices – be they mobile phones, smartwatches or even electric vehicles – having to be built around the battery.
This can often lead to wasted internal space and contribute to less than innovative exterior designs, given the limitations provided by a lithium-ion battery’s shape.
But a team of researchers from Duke University in North Carolina are looking to revolutionise the world of lithium-powered devices with the idea of creating custom-sized lithium-ion batteries using 3D printing technology.
In new research published in the ACP Applied Energy Materials, postdoctoral researcher Christopher Reyes and Associate Professor of Chemistry Benjamin Wiley explained the ability to 3D print lithium-ion batteries in an “arbitrary geometry” would allow a battery’s “form factor” (or shape) to be customised to fit a product’s design aesthetic, while facilitating the use of the battery as a structural component.
A 3D printer would produce the electrolyte and two electrodes (the cathode and anode) in one process, compared to the current lithium-ion production scenario where the three elements are manufactured separately and combined inside a casing.
Cutting-edge ink mix
Not just any printer will do though, as the polymers used in conventional 3D printers, such as poly(lactic) acid, are not ordinarily conductive and therefore unable to duplicate the electric current technology used by lithium-ions.
In their research article, Reyes and Wiley explained how they infused the polylactic acid with a mixture of ethyl methyl carbonate, propylene carbonate, and lithium perchlorate to obtain an ionic conductivity comparable to that of polymer and hybrid electrolytes.
The result was a cutting-edge chemical ink mix which could enable 3D printing of complete lithium-ion batteries to any shape or size using low cost and widely-available fused filament fabrication (FFF) machines.
To prove their battery breakthrough, the team 3D-printed an LED bangle complete with custom-sized lithium-ion battery where the anode and cathode were printed as freestanding curved electrodes which matched the contour of the bangle.
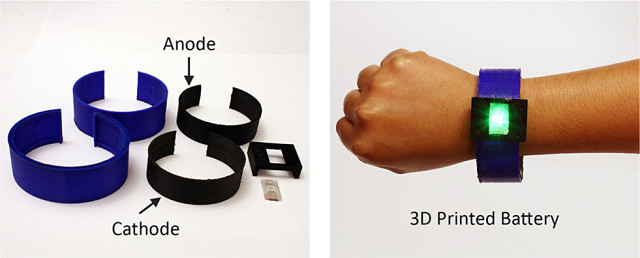
The lithium-ion battery powered LED bangle that was 3D printed by the team at Duke University.
A Celgard polymer separator was used in the device to improve the performance of the battery and demonstrate the ability to integrate 3D-printed battery technology with existing materials.
After infusion and assembly, the bangle battery could power a green LED for approximately 60 seconds.
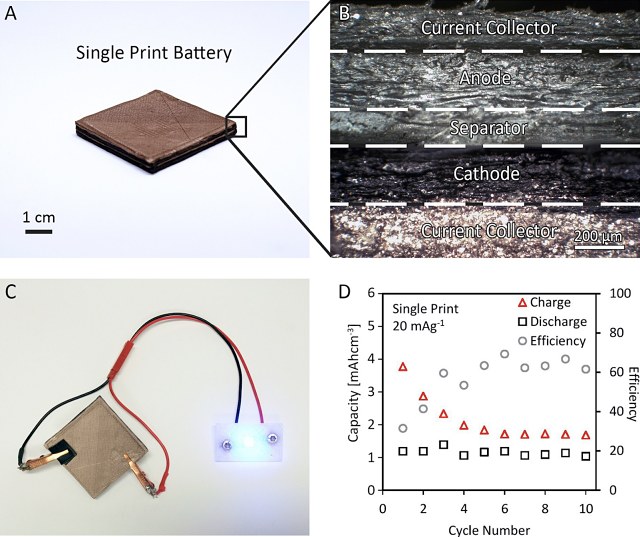
The 3D printed battery was created in a single print by exchanging the filament at predetermined layer heights, the battery was then vacuum filled with electrolyte.
According to the article, the capacity of the first-generation 3D-printed battery is “about two orders of magnitude lower than that of commercial batteries”, and too low for practical use.
A microlattice approach
Over at Carnegie Mellon University in Pennsylvania, a team of mechanical engineering researchers have developed their own take on 3D battery printing, with the view that lithium-ion battery capacity can be vastly improved if, on the microscale, their electrodes have pores and channels.
The team is using a microlattice structure to improve the capacity and charge-discharge rates for lithium-ions, representing a major advance in printing complex geometries for 3D battery architectures as well as an important step toward geometrically-optimising 3D configurations for electrochemical energy storage.
They estimate the technology will be ready to translate to industrial applications by 2020.
“In the case of lithium-ion batteries, the electrodes with porous architectures can lead to higher charge capacities,” said Carnegie’s associate professor of mechanical engineering Rahul Panat.
“This is because such architectures allow the lithium to penetrate through the electrode volume leading to very high electrode utilisation, and thereby higher energy storage capacity.”
While up to 50% of the total electrode volume in normal batteries is not utilised, the microlattice invention allows the efficient transport of lithium through the entire electrode, which also increases battery charging rates.
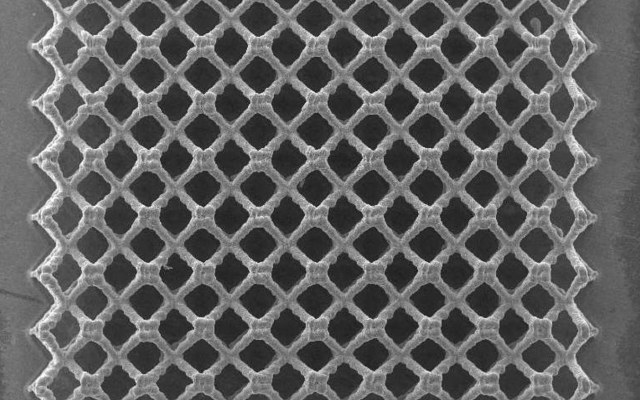
The 3D-printed microlattice structure used by the Carnegie Mellon University to achieve higher charge capacities.
Professor Panat and his team developed their own 3D printing method to create the porous microlattice architectures, while leveraging the existing capabilities of Aerosol Jet 3D technology created by US-based Optomec.
Aerosol Jet technology enables 3D printing of electronic components such as resistors, capacitors, antennas, sensors, and thin film transistors.
Performance characteristics of printed components, for example the ohm value of a resistor, can be controlled through printing parameters and components can also be printed onto 3D surfaces, eliminating the need for a separate substrate and reducing the size, thickness and weight of the end product.
3D battery printing will have significant benefits in areas such as consumer electronics, biomedical devices (where miniaturised batteries are required), and aerospace applications, due to the low weight-high capacity nature of the batteries and their ease of transport.
The lithium lowdown
Lithium and lithium-ion batteries provide portable electricity, with the main difference being that lithium is a primary cell (not rechargeable) offering higher capacity and density than lithium-ion, which is a secondary cell and can be charged over and over before becoming ineffective.
Lithium technology has been brewing since the 1970s but took the market by storm in 1991 when Sony Corporation released the first commercially-available lithium-ion batteries, transforming the electronics market with a major improvement in energy density and kickstarting a new era of (albeit clunky) portable phones and computers.
Lithium battery technology has been instrumental in the drive towards a greener planet, with its lightweight, energy-dense and rechargeable properties making the batteries ideal candidates for the global electric vehicles market.
The latest Nissan Leaf battery, for example, is claimed to use materials which can store a higher density of lithium-ion – meaning customers can drive an even greater distance in their new generation cars.
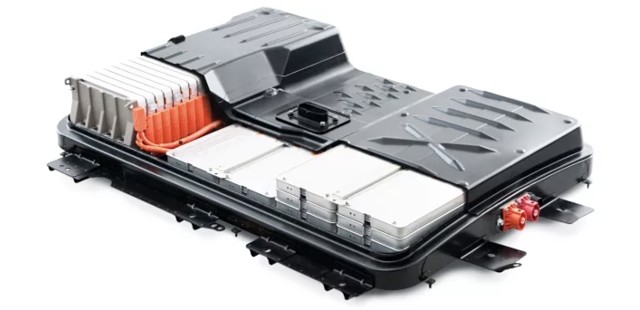
The Nissan Leaf battery allows for long distance travel.
And instead of becoming hazardous waste when the batteries lose their charge, the world’s foremost users of electric vehicles are already introducing strategies to manage expired batteries and keep them out of landfills.
The European Union requires electric vehicle batteries to be recycled at the end of their life, while Nissan announced a plan earlier this year to give its Leaf batteries a second life by using them to store energy for off-grid street lamps in Japan.
Attached to a solar panel, the second life batteries charge during the day and power streetlights at night.
Car manufacturers worldwide are launching similar energy storage strategies to re-purpose old lithium-ion batteries – with the exception of Tesla, which has long questioned the belief that spent batteries can be reliable and predictable enough to deploy back into a grid setting.